Duplex Stainless Steel
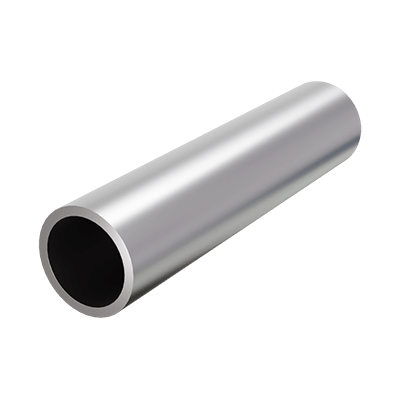
Duplex Stainless Steel
Duplex stainless steels are two-phase microstructure alloys having both ferrite and austenite grains in their microstructure. The austenite in the grain form is surrounded by the ferrite phase in about equal proportions. The result is a grade with higher overall strength, better corrosion resistance, and a value for money in regard to the properties provided. Duplex stainless steels are used in applications where thinner sections are required. The Duplex grades use a combination of ferritic steel and austenitic steel properties like high strength and ease of fabrication respectively. Their common applications include oil and gas industry, marine applications, and applications involving aggressive chemical environments.
Not able to find what you are looking for?
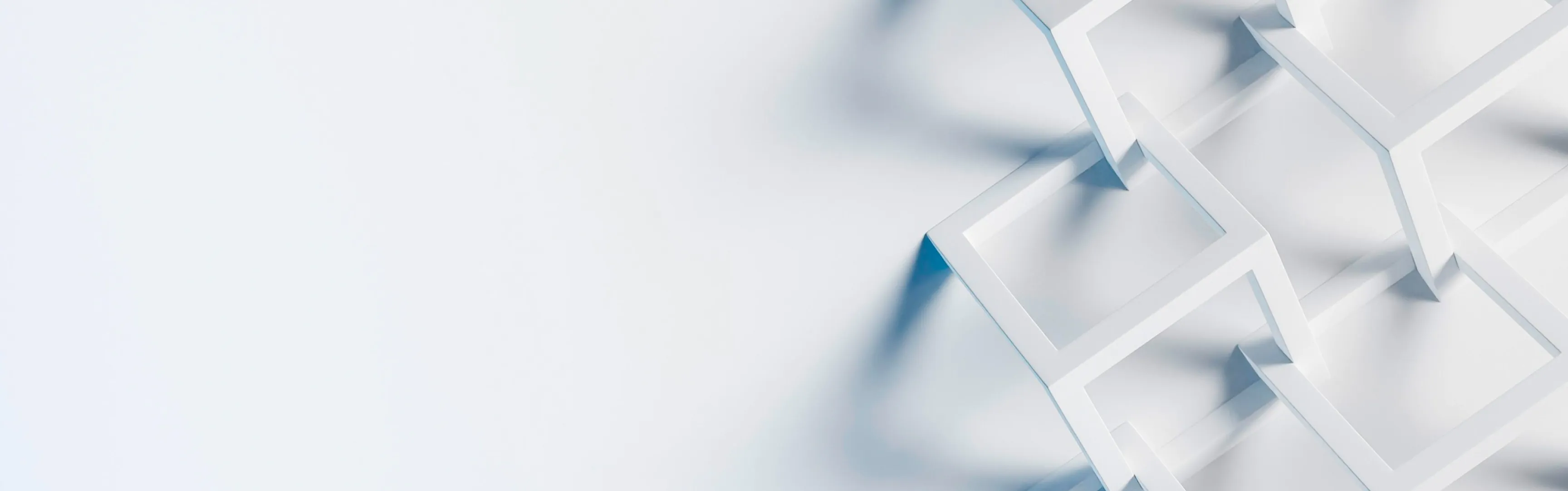
Manufacturing Capabilities
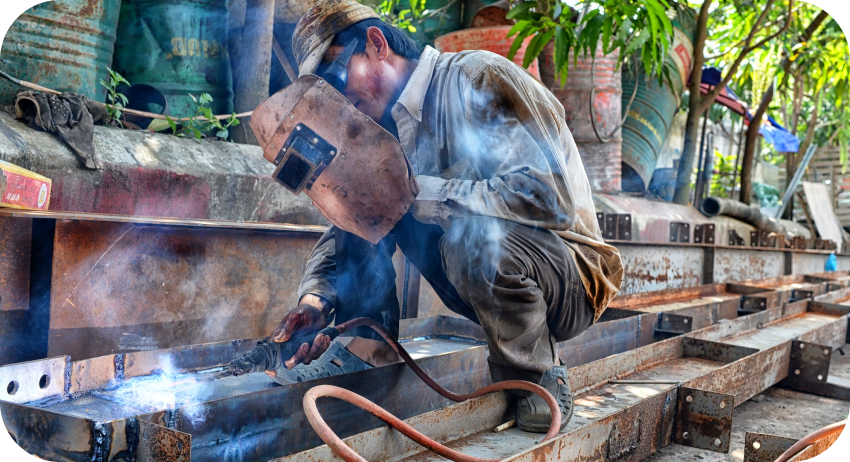
Cold Pilgering
Seamless pipes can be manufactured either by extrusion or piercing. Of which, extrusion is a widely known process because it provides a uniform outer diameter and concentric inner diameter and is the only process that is suitable for long-length seamless tubing. This process is different from ERW pipes since it does not have a welded joint along their length and can be extruded to any desired length. The raw material is collected in the form of hot extruded seamless pipe which is then supposed to be cold reduced. The process of drawing a tube to a particular size includes the shrinking of a large diameter tube into a smaller one, by drawing the tube through a die. The result of this process is high quality tubing with precise dimensions, excellent surface finish, and the added strength of cold working. The process used in tube reduction is known as Cold Pilgering. There are two important facts about the pilgering process – First, pilgering is a cold working process and therefore it greatly improves the material structure. Second, it can cut down a large amount of outside diameter, inside diameter and thickness of the tube with a reduction rate of 50-60%. The equipment includes a saddle assembly which holds the pair of dies- upper die and lower die. These dies are forced over the tube’s outer diameter. There is a mandrel inside the tube which maintains its inside diameter while the dies reduce its outer diameter. The mandrel is tapered and stationary but does rotate at specific time in a cyclic process. Due to the forcing of the dies in between the tube, its lateral dimension decreases whilst its longitudinal dimension increases. That is why, the tube obtained is considerably longer. The process is then followed by degreasing and drying of the pipe so that the heat treatment on the metal can be appropriately carried out. The heat treatment process used on the pipe is annealing, which includes heating of the pipe to a temperature, maintaining that temperature for a certain period of time and then cooling. Annealing becomes important since it gives the metal its required toughness and removes internal stress from the drawing process. The metal pipes then go through the straightening process in the presence of rollers, for the purpose of levelling and removing any deviations. The approved seamless metal pipes undergo the process of cutting and deburring. The cutting operation cuts the tube to required lengths and the deburring process removes any and all burs. Both of these operations are carried out for the purpose of improving the surface finish and removing all sort of surface impurities such as stains, contaminants, rust, etc. The processed product goes to the testing department where one or more non-destructive tests are carried out. These test includes hydrostatic testing and eddy current testing. Hydrostatic testing detects the strength of the metal as well finds out for any leaks in the pipe. Eddy current test detects any surface as well as subsurface flaws in the pipe. Mechanical tests may include tests for hardness and yield strength. Finally, there is a quality check done by the quality control department after which the product is packed and shipped. Being ISO 9001: 2008 certified company, Shalco Industries has always strived to provide their customers the highest quality of products.
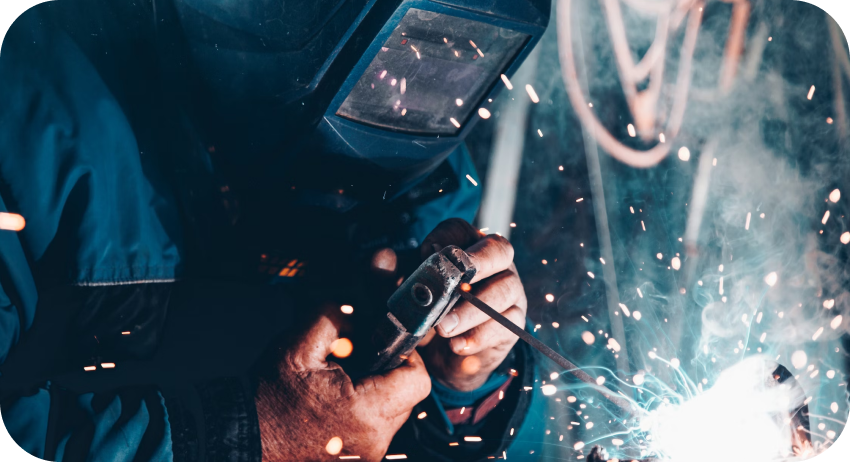
Draw Bench
Seamless pipes after being extruded are produced by cold processing methods like Cold Pilgering and Cold Drawing. Cold Drawing is a comparatively slower process and gives lower reduction ratio of about 15-35% depending on alloys, but give a very fine and commendable grain structure. Both manufacturing processes have their own advantages depending upon the need. Cold working also has an advantage of quicker tool changes and low operational costs. Cold drawing is basically a metal working process where the metal is stretched by using tensile forces. Since it is done at room temperature, it is known as cold working. The principle used here is quite similar to cold pilgering where, the desired size of the pipe is achieved by forcing it between dies, reducing the lateral dimension of the pipe, i.e. diameter and increasing the longitudinal dimension, i.e. length. The machine used for the purpose is known as Draw Bench. Draw bench uses only pressure and no heat to change the shape of the metal by cold working on steel. The drawing begins with procuring of raw materials with care to be taken about the material’s chemistry and dimensions including tolerances—size, wall thickness, concentricity, and straightness. The next process is pointing, which includes reduction of the material’s diameter at the tube end so that it can enter die. The common methods are push pointing, rotary swaging, and squeeze pointing. The draw bench is usually mechanical with a back bench, die head and front section. The cold drawing reduction process involves two types – one with mandrel inside the tube known as Rod drawing and one without mandrel known as sink drawing. In rod drawing, a hardened steel mandrel is inserted inside the pipe followed by a gripper. The outer diameter of the pipe is determined by the size of the die and the inner diameter is determined by the size of the mandrel. After the tube has been introduced into the die, lubricating oil is pumped on the surface. Advantages of rod drawing are that drawing speeds are good enough and appreciable amount of reduction ratio can be obtained. Here, both the outer diameter and the wall thickness are reduced. This is not the case in Sink drawing, where the pipe is drawn from the die without any mandrel or internal support. This causes reduction in outer diameter without affecting wall thickness to a great extent. This method can be used to draw the tube to a finished size and is also performed as a sizing pass after rod draw. The proper die angle will depend upon diameter to wall thickness ratio. The drawing of the tube in the die would involve considerable amount of friction and might result in unwanted wear, for this reason appropriate amount of lubrication needs to be provided, chlorinated oils are generally used for this purpose. The drawn product or the Cold Drawn pipe, exhibits a bright and polished finish, increased mechanical properties, improved machining characteristics and precise as well as uniform dimensional tolerances. Furthermore, annealing can be used for heat treatment in removing internal stresses and softening the product. After all the processes are completed, the final product is packed, shipped and delivered.
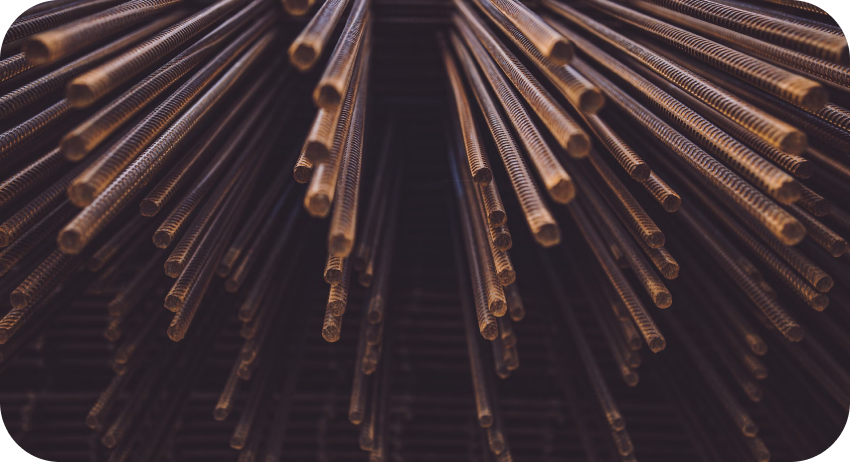
Hot piercing mill
Seamless pipes are manufactured by a number of cold as well as hot rolling processes. The hot rolling process used to manufacture pipes at about 1250-1300 deg. Celsius is known as Hot Piercing process. The piercing is carried in a plant known as the piercing mill, which consists of a number of dies, of which, two primary contoured work rolls rotate in the same direction with their axes at 3 to 6 degree with respect to the horizontal stock plane. The process is also known as rotary piercing or seamless tubing. A conditioned steel round of appropriate weight, grade and diameter is heated to a suitable forging temperature which is to be pierced in one or two of the mills. Rotary hearth furnace is usually used in the process to heat the steel into a round or a billet shape. These steel pieces are already cut in their required lengths and are indexed and arranged according to the customers’ requirements. The billets are then given a 1-inch indentation by billet centering machine at its one end to act as a starting point for rotary piercing. This indentation aids the piercing tool during actual tube formation. Rotary piercing is a dynamic and a rapid process that produces the tube shell in just a few seconds. As the billet passes in between the cross rollers, the mandrel or the piercing roll tool gives the billet its tube shape by piercing the billet through its centre. The process makes the material elongate between 1.5 to 2 times and reduce its cross section between 33 to 50%. The cross rolling of the billet causes high tensile stress at the centre of the billet. The load imparted by the roller makes sure that the rotation and translation is happening at its core segments. The design of the piercer roll makes the metal flow over the piercer point and to the exit of the process. The piercer point is a high-temperature, water-cooled alloy tool, with a design to allow the metal to flow over the piercer roll as a tube shell form. The piercing point is attached to a rod which stays in its place after rolling. The roll gap is usually closed by a non-driven support roll at the top and a support shoe at the bottom. After the piercing of the tube, if required, it can go through a pilgering process for the purpose of cold reduction. After the processing, the pipes are brought to a cut-to-length mechanism where they are cut to a required length. The material is then brought to its required yield strength with appropriate heat treatment method. The features of this process involve two aspects – one is that the process results in a seamless tube that is homogenous in microstructure and physical properties, second is that the process involves high production of standard seamless pipes to be used specifically in oil and gas industries.
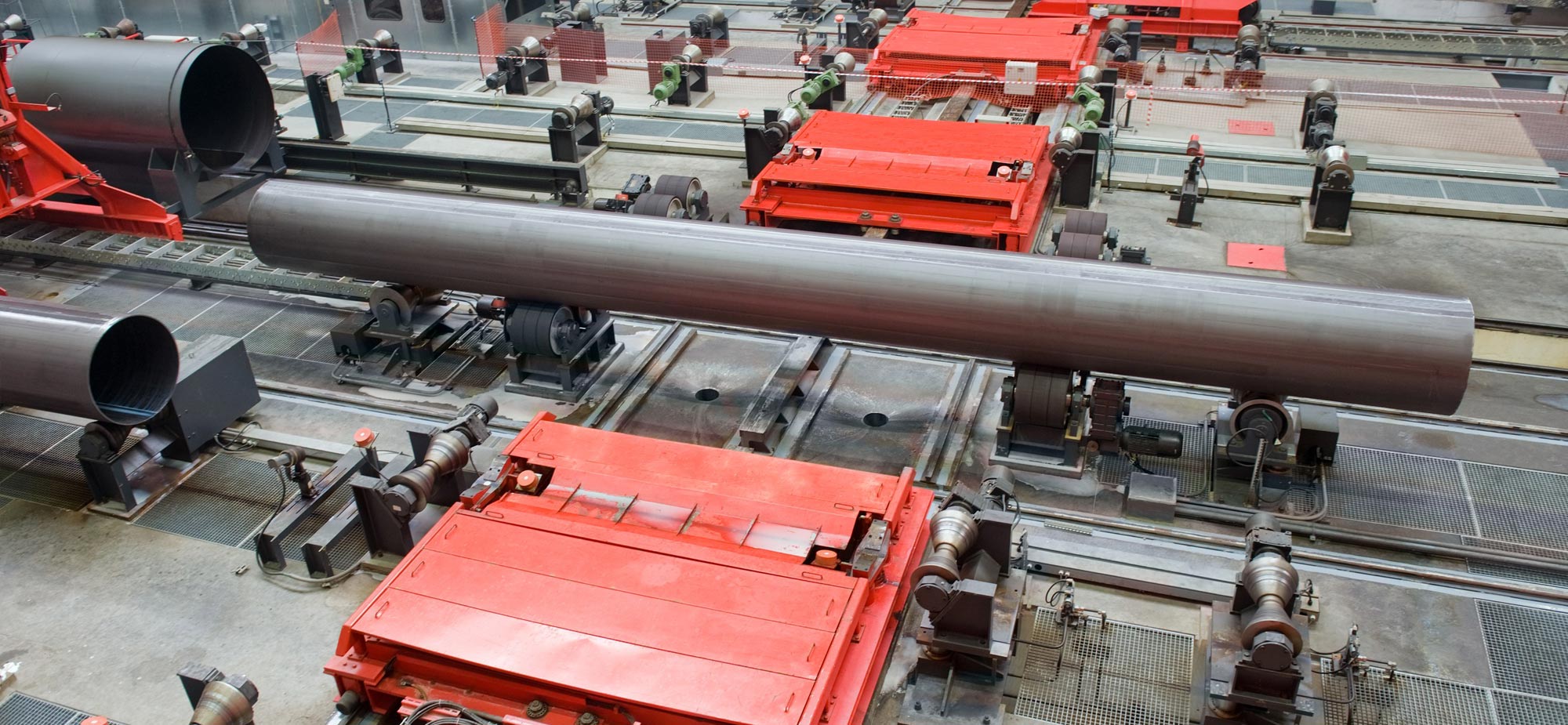
TUBE MILL
The manufacturing of welded pipes and tubes is a significant part of precision engineering. Immense care is taken to maintain the dimension and strength of the products. The same tolerance is sustained throughout the procedure to provide you quality standards products. At its premature stage, the metal is obtained in the form of coils of specific thickness. The metal coil is then inspected before processing. The quality requirements of the raw material are governed based on technical parameters and specifications. The metal coil is levelled for deviations, and if any, it is brought to appropriate thickness. The next operation performed on the coil is slitting. The length of the metal coil is cut in several sections either by carbide cutters or saw blades of superior quality. These strips of the metal coil are tested with ultrasonic to see for any flaws before processing. The ultrasonic waves are set to appropriate frequency, high sensitivity, and high penetrating power that are then transmitted into the coil to detect flaws of all types. With this process, even the miniscule flaws can be identified and removed. The inspection process thereby becomes automated and the results are immediate, making the process smoother and faster. The condensed strips then undergo preliminary forming. The rollers of specific shapes are placed in alignment to give the metal its tubular shape. The shape of the pipe is obtained along the process line. The pipe is welded along its length under a specific pressure to gain its tubular shape, the welding of the pipe makes it strong and uniform. Therefore, the welding technique is vital for the process. The integral part used in welding is the Electric resistance welding, (ERW) which operates on electric current, the heat generated from the electric resistance acts as a power source to conduct welding. The required pressure is provided by the electrodes. As the current is passed through the electrodes, resistance by the metal to the current increases the heat and the required butt weld is formed. ERW has high energy efficiency, high productivity, less inconsistencies, easy automation, and no metal filler requirements unlike conventional welding techniques. Welded pipes and tubes are also often called ERW (Electric Resistance Welded) pipes. The formed pipes are once again checked under Ultrasonic equipment. And to remove internal stresses caused during the welding process the metal pipes are gone through a heat treatment called annealing. This process involves heating the metal above its recrystallization temperature, maintaining it for a suitable period and then cooling it, this will improve the metal’s ductility or toughness. The pipe after getting its strength from annealing and water cooling goes for in-line process of sizing, fly cutting and straightening. A precise dimension is obtained after these processes. Now to finally obtain its accuracy, the pipe is gone through hydrostatic testing and eddy current testing. Hydrostatic testing detects the strength of the metal as well as finds out for any leaks in the pipe whilst Eddy current test detects any surface and subsurface flaws. The thoroughly examined welded pipe and tubes are finally weighed, measured and packed for usage.