Duplex SS 2205
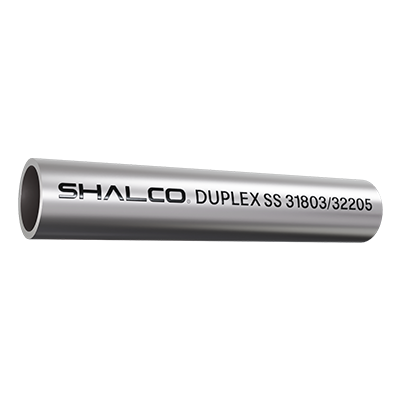
Duplex SS 2205
Duplex stainless steels are two-phase alloys with austenite and ferrite phases in their microstructure in nearly equal proportions. The result is a component with better strength, better mechanical and better corrosion resistance properties as compared to most of the standard austenitic alloys. The grade SS 2205 is a modification of grade 31803 -- modified in the year 1996, to enhance specific properties like corrosion resistance, toughness, etc. The use of the grade has a limitation in its temperature. When heated above 300°C, the grade forms carbide microconstituent precipitation in the grain structure and when cooled below -50°C, the component gets hardened, resulting from ductile to brittle transition of the microstructure.
The grade has nitrogen addition to provide strength and avoid common corrosion problems in the austenitic 300 series. The microstructure of the grade comprises of ferritic phase surrounding the austenitic phase.
Ferritic alloys have higher strength and better corrosion cracking resistance while austenitic grades have better machining properties and general corrosion resistance, pertaining to the difference in the content of iron, carbon and other alloying elements. The duplex grade 2205 combines the properties of both the phases. Therefore, it can be argued that 2205 is the most widely used duplex stainless steel. It has outstanding fatigue strength along with double the yield strength of austenitic grades, which allows the grade to be used in various dynamic applications. It can be sectioned, fabricated and weighed as per the designer’s consideration. Localized as well as uniform resistance to corrosion is provided in environments from moderate to severe corrosion conditions.
The localized corrosion like pitting and crevice corrosion performance of the grade is better than grades, 316L and 317L of 300 series. The grade also has lower thermal expansion comparatively. Hence, during welding, there is little to no expansion of the base metal at the heat affected zone and the grade also demonstrate enhanced welding properties. Balanced welding properties are maintained even at the heavier sections of the grade. The excellent ductility and the composition of 2205 are the key elements to forge the grade as per the needs of the application. Hot forming as well as cold forming can be suitably done on the grade.
Hot forming needs to be carefully and uniformly done in the range 950-1150°C. At this range, the matrix becomes soft and is easily formed. Below this temperature, the grade becomes more prone to austenitic structure than ferritic, moreover, if the shape is not uniform, the corners may be cooler than other areas resulting in the formation of cracks. Also, there might be a formation of intermetallic phases below 930°C. The intermetallic phases in the grade severely deteriorate the grade's corrosion resistance, mechanical and welding properties. It needs to be completely annealed so as to restore its properties and use it in applications. The grade has very high strength and work-hardening rate due to which cold forming requires higher forces. Even allowances are required for the spring-back of the grade due to its strength. The grade 2205 makes its way in most of stainless steel applications because of its varying properties and versatility stemming from its two-phase structure.
Physical Properties
General Specification
Standards Specifications
Pipes & Tubes
Fittings & Flanges
Forms of Supply
Piping and tubing, fittings and flanges, washers.
[#corrosion-resistance]Corrosion Resistance[#corrosion-resistance]
The grade has improved resistance to various forms of corrosion than most of the 300 series alloys. They prove to be cost-effective in many ways. Chloride stress corrosion resistance can be provided up to 150°C. However, the grade cannot perform well at higher temperatures. The chromium, nitrogen, nickel, molybdenum content in the grade provides resistance to various media. Superior resistance to localized corrosion is provided in highly oxidizing as well as acidic conditions. Exceptional corrosion fatigue resistance is provided along with high strength and resistance in aggressive mediums. The grade is thereby used in many applications.
[#fabrication-and-heat-treatment]Heat Treatment[#fabrication-and-heat-treatment]
The grade is suitably heat treated by annealing at around 1040°C, followed by rapid cooling. Annealing is done after the process to retain the required properties and remove internal stresses efficiently. Stress relieving below this temperature might carry the danger of forming intermetallic phases on the borders and hence it is avoided.
[#weldability]Weldability[#weldability]
The grade can be suitably welded using conventional welding techniques like gas tungsten arc welding, gas metal arc welding, shielded metal arc welding, submerged arc welding, etc. Formation of the excessive ferrite phase at the weld can be avoided with appropriate filler metal. Formation of the intermetallic phases at the heat affected zone of the weld can be avoided when appropriate welding technique is used.
Machining
High speed tooling and carbide tooling can be used. The grade has superior toughness than other 300 series alloys but is slightly difficult to machine. Work hardening takes place inside the layers of the grade. Powerful machinery with rigid tooling becomes imperative. Therefore, cutting speeds are kept low and adequate lubrication is provided.
[#applications]Applications[#applications]
Effluent scrubbing systems, Food processing equipment, Flue gas desulfurization equipment, Marine and other high chloride environments, Chemical processing, digesters, bleaching equipment, and stock-handling systems, transport and storage, Oil and gas exploration and processing equipment, Biofuels plants, Cargo tanks for ships and truck, Rotors, fans, shafts, and press rolls.
Possible grade alternatives
More related products
Not able to find what you are looking for?
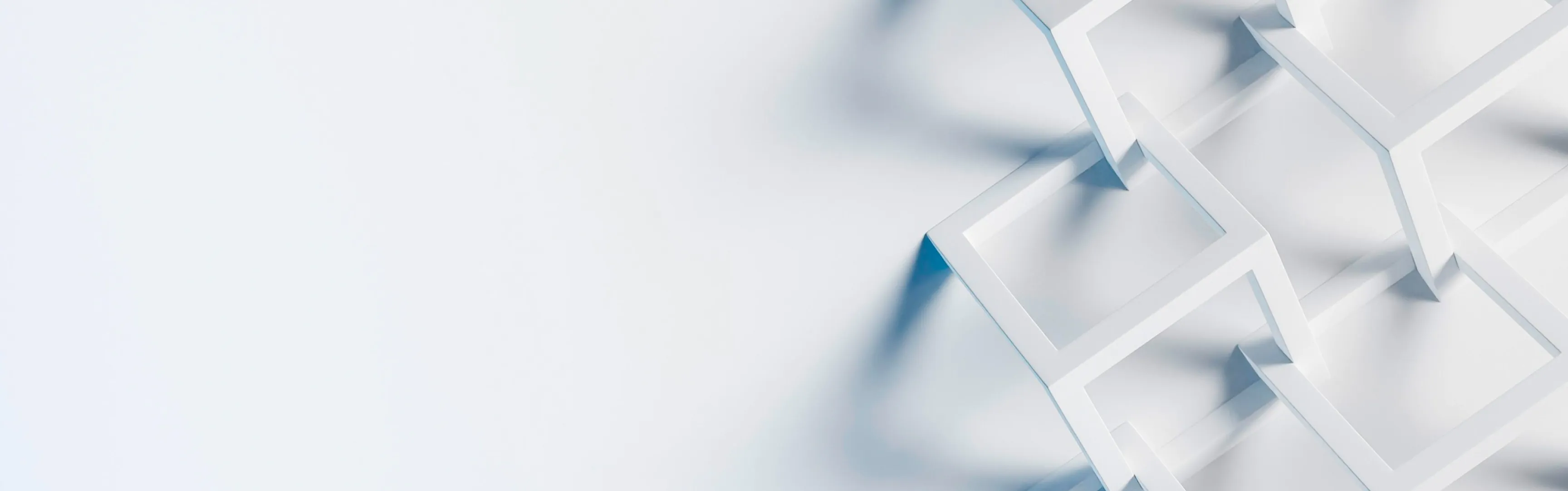