Copper nickel 70-30
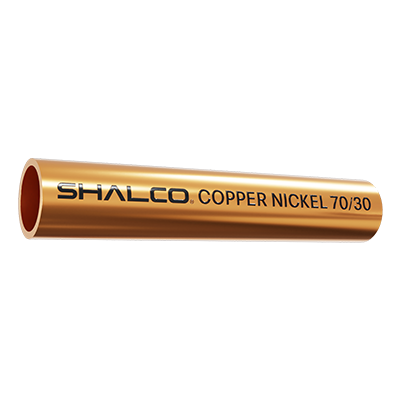
Copper nickel 70-30
Copper nickel alloy 70/30 is a premium-grade alloy composed of 70% copper and 30% nickel, along with small amounts of iron and manganese. These additional elements enhance the alloy’s corrosion and erosion resistance, making it more durable and reliable than alloy 90/10. Copper nickel alloy 70/30 also offers slightly enhanced strength, making it an excellent choice for demanding applications in marine, chemical, and power generation industries. One of the standout features of Copper 70/30 is its excellent resistance to oxidation and stress corrosion cracking. This nickel alloy 70/30 performs exceptionally well in moist air and steam environments, where its high oxidation resistance ensures longevity. Additionally, it maintains thermal stability and mid-level strength even at elevated temperatures, making it suitable for challenging operating conditions.
Physical properties
[#fabrication-and-heat-treatment]Fabrication and Heat Treatment[#fabrication-and-heat-treatment]
Alloy copper nickel 70/30 reacts well to most fabrication processes and can be readily hot and cold worked. It is also easily joined by brazing, soldering, or even with other welding methods. With good hot and cold forming ability and malleability approaching that of copper, copper nickel 70/30 does not harden instantly, letting the material draw and spin.
CuNi 70/30 or UNS C71500 alloy can be annealed at specific temperatures between 649°C and 816°C (1200°F and 1500°F). In the annealed condition, copper nickel alloy offers moderate strength levels which makes it perfectly suitable in more demanding applications. Copper nickel alloy also has good fabricability as mentioned above and high inherent resistance to biofouling.
Alloy copper nickel 70/30 is renowned for its excellent adaptability to various fabrication processes, making it a popular choice across numerous industries. This alloy can be readily hot and cold worked, demonstrating malleability close to that of pure copper. With its good forming abilities, copper nickel alloy 70/30 can be drawn and spun effectively without instant hardening, allowing manufacturers to shape it into complex components with ease. Additionally, the alloy is easily joined using brazing, soldering, and other welding methods, further enhancing its appeal for demanding applications.
The thermal properties of copper nickel alloy 70/30 are also noteworthy. Annealing the CuNi 70/30 alloy (UNS C71500) at specific temperatures between 649°C and 816°C (1200°F and 1500°F) improves its ductility and maintains moderate strength levels. These properties make nickel alloy 70/30 highly suitable for use in environments requiring both durability and flexibility.
Moreover, the alloy's inherent resistance to biofouling sets it apart from other materials, ensuring longevity and low maintenance. Copper nickel 70/30’s combination of strength, fabricability, and resistance to environmental factors makes it a reliable solution in marine, industrial, and architectural applications.
Alloy copper nickel 70/30 stands out as a versatile and durable material, balancing performance and workability for a range of industries.
[#corrosion-resistance]Corrosion Resistance of copper nickel alloy[#corrosion-resistance]
Copper nickel alloy 70/30, also known as cupronickel, is widely recognized as one of the most corrosion-resistant and durable copper-based alloys. It is extensively used in condensing and heat exchanging tubes in seawater environments. This alloy copper nickel 70/30 offers exceptional resistance to corrosion, erosion, and pitting, making it highly suitable for applications in harsh marine conditions. Additionally, it exhibits excellent strength, workability, and weldability.
The corrosion resistance of copper nickel 70/30 is notably enhanced in high-velocity waters (up to 4.5 m/s) and even in contaminated or polluted seawater. Nickel alloy 70/30 also demonstrates impressive resistance to stress corrosion cracking, corrosion fatigue, and maintains its mechanical properties from sub-zero temperatures to around 300°C. These qualities make alloy copper nickel 70/30 a reliable material for demanding applications in challenging environments.
Beyond marine environments, CuNi 70/30 alloy excels in resisting corrosion caused by freshwater, boiler feedwater, and steam. Its resistance extends to attacks by phosphoric, sulfuric, and mild organic acids. Copper nickel alloy 70/30 also stands out for its superior resistance to alkaline chlorides, chromates, nitrates, and sulfates. Furthermore, nickel alloy 70/30 is impervious to wet and dry chlorine, bromine, and carbon dioxide at ambient temperatures, further enhancing its versatility and reliability.
Copper nickel 70/30 offers a unique combination of corrosion resistance, durability, and mechanical stability. Alloy copper nickel 70/30’s superior performance in marine and industrial applications reinforces its reputation as a preferred material in environments where reliability and longevity are critical.
Specifications
[#applications]Applications[#applications]
UNS C71500 alloy is used in applications where stainless steel cannot be utilized as chloride stress-corrosion cracking may occur and other parts may require high corrosion resistance.
Cupronickel alloy has widely been used in the marine sector that has since extended to industries including:
- Offshore oil and gas
- Power generation
- Desalination
- Cooling plants.
The alloy is commonly used for seawater service as forged and machined valve and pump components, flanges, fittings, and hardware due to its inherent corrosion resistance and also areas where high corrosion resistance is needed and the issue of chloride stress-corrosion cracking limiting the use of stainless steels.
- Submarine and seawater pipework
- Offshore firewater systems
- Heat exchangers
- Condensers
- Sheathing of legs and risers on offshore platforms
- Boat hulls
- Hydraulic lines
- Desalination units
NOTE: Copper nickel 70/30 is a registered trademark of Special Metals Corporation.
More related products
Not able to find what you are looking for?
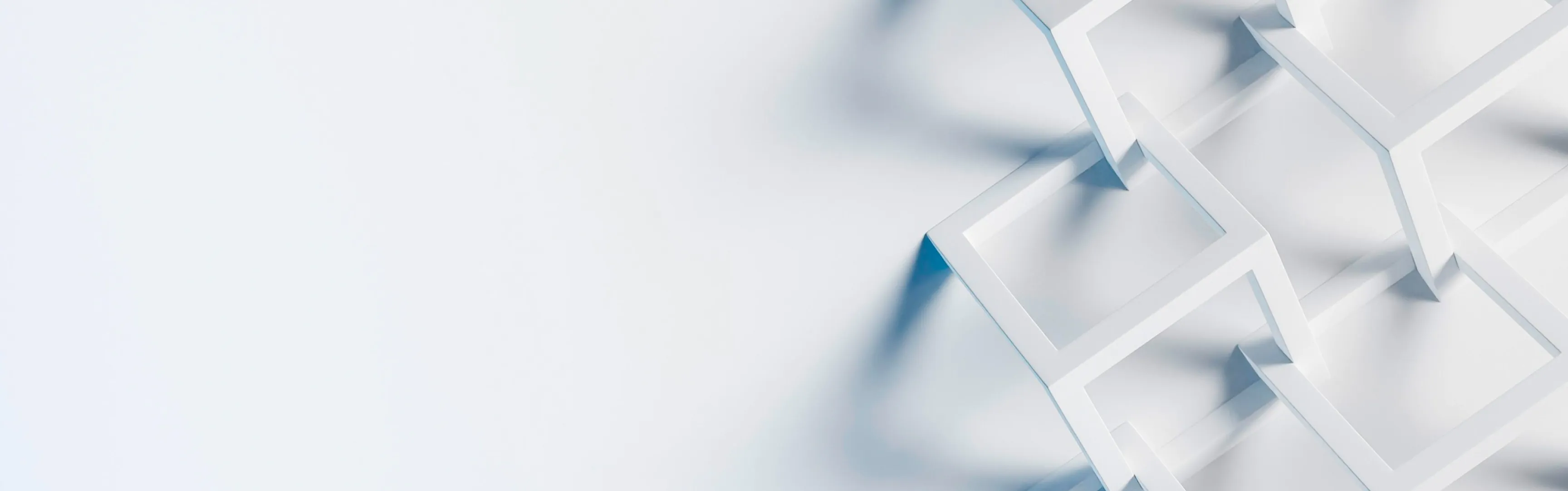