Austenitic SS 316
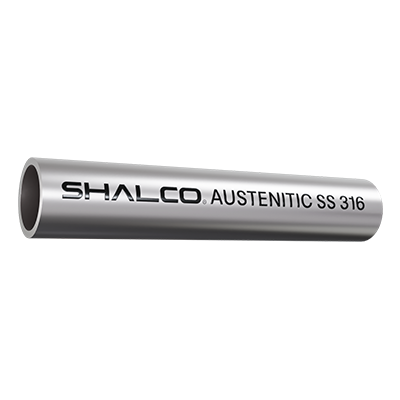
Austenitic SS 316
SS316 steel is an austenitic chromium-nickel stainless steel that contains between 2 and 3% molybdenum. 316 Stainless steel has better corrosion properties due to its molybdenum content which improves its resistance to pitting in chloride ion solutions and makes it strong for higher temperatures. SS Grade 316 is an Austenitic standard molybdenum-bearing grade, which is very useful stainless steel and is highly resistant to general corrosion. Austenitic SS316 is better than the conventional nickel chromium stainless steels such as 302 and 304.
SS316 Composition
When unfolded, the SS316 composition reveals that the molybdenum content in it gives it better corrosion resistance when we compare 304 Vs 316 Stainless steel. This comparison is proven particularly as higher resistance to pitting and crevice corrosion in chloride environments. SS316 and SS304 have excellent toughness due to the austenitic structure even down to cryogenic temperatures.
One might find plenty of variety of type 316 stainless steel. Some of the popular types remain the L, F, N, and H variants. Each is slightly different, and each is used for different purposes. The difference of the “L” designation suggests less carbon content in 316L when compared to 316. Alloy 316 & 316L have excellent elevated temperature tensile, stress-rupture strengths and creep, and extra-ordinary formability and weldability.
When we compare SS304 Vs SS316, both are similar and used widely in the food industry, both type 316 and 316L have better corrosion resistance and have better strength at elevated temperatures. Just have an example of SS 316 coil; it’s widely used and similarly popular. Both are non-hardenable even in heat treatment and are ready to form and draw pulled or pushed with the use of a die or a smaller hole.
SPECIFICATION
Grade SS 316 L, which is the low carbon version of SS 316 steel and is resistant to sensitization i.e. grain boundary carbide precipitation. Thus, it is widely used in heavy gauge welded materials over about 6mm. Grade 316H, is a higher carbon version of SS316 and has application at elevated temperatures, as does its stabilised grade – 316Ti.
SS 316 Physical Properties
SS316 is excellent in a range of atmospheric environments and many corrosive media – generally more resistant than 304. Considering the pitting and crevice corrosion in warm chloride environments, and in above about 60 °C to stress corrosion cracking. ITP SS316 is considered resistant to potable water with up to about 1000 mg/L chlorides at ambient temperatures, reducing to about 500 mg/L at 60 °C.
PHYSICAL PROPERTIES
Stainless steel 316 has good oxidation resistance in intermittent service to 870 °C and in continuous service to 925 °C. Regularly using 316 in the 425-860 °C range is not usually recommended if relevant aqueous corrosion resistance is needed to be maintained. The main difference between SS316 and SS 316L is that grade 316L has better resistance to carbide precipitation and it can be further used in the above mentioned temperature range.
[#fabrication-and-heat-treatment]Alloy 316 Heat Treatment[#fabrication-and-heat-treatment]
Alloy 316/316L in annealed conditions is non-magnetic, but can become slightly magnetic as a result of cold working or welding. Alloy 316 and 316L are good in easy welds and process by standard shop fabrication practices. SS316 undergoes solution annealing process in temperature range of 1010-1120 °C and then cool rapidly. These grades cannot be hardened by thermal treatment.
[#weldability]Alloy 316 Weldability[#weldability]
SS316 has excellent weldability by all standard fusion methods, both with and without filler metals. Grade 316 in heavy welded sections need post-weld annealing to maintain better corrosion resistance. This is not required for 316L. Grade 316Ti can also be used in place of 316 for heavy section welding.
Not able to find what you are looking for?
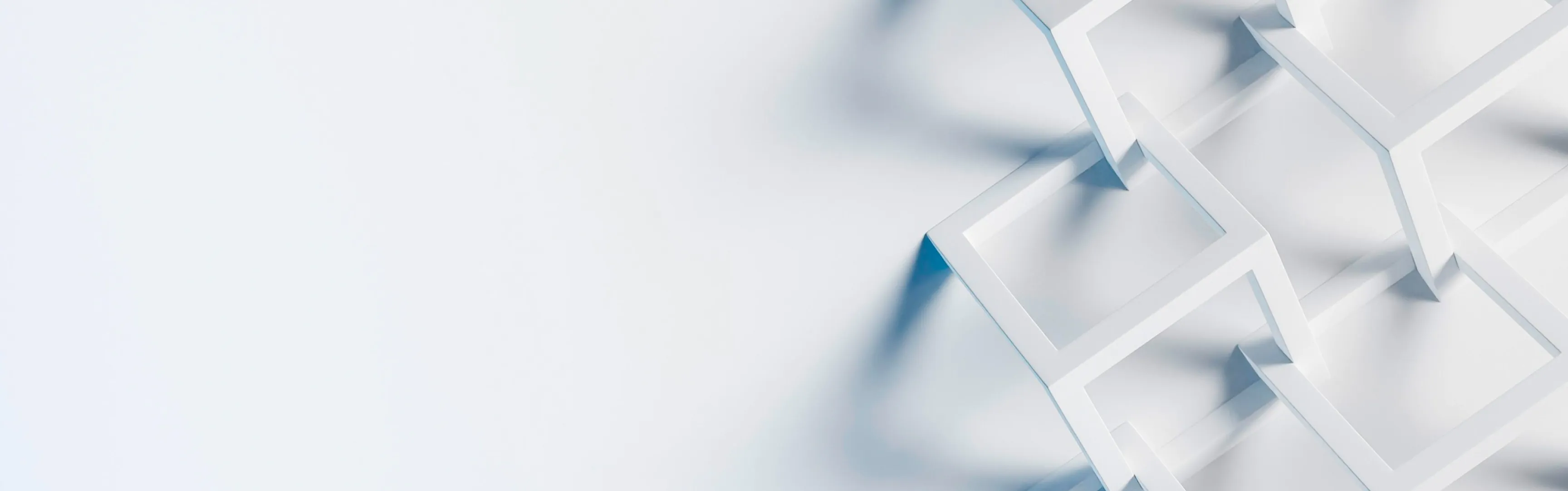